The skies have always symbolized humanity’s relentless pursuit of innovation. Today, that pursuit is taking a quantum leap forward as aircraft assembly automation transforms how planes are built, tested, and delivered. Gone are the days of purely manual labor dominating hangars—welcome to an era where robots collaborate with engineers, AI optimizes workflows, and precision is measured in microns. Let’s explore how this technological revolution is reshaping aerospace manufacturing.
**The Dawn of a New Era in Aircraft Production**
Imagine a factory floor where robotic arms seamlessly install fuselage panels, autonomous vehicles transport components without human guidance, and augmented reality (AR) headsets overlay digital blueprints onto physical structures. This isn’t science fiction—it’s the reality of modern aircraft assembly. Automation has become the backbone of aerospace manufacturing, addressing challenges like labor shortages, complex design requirements, and the need for unprecedented accuracy.
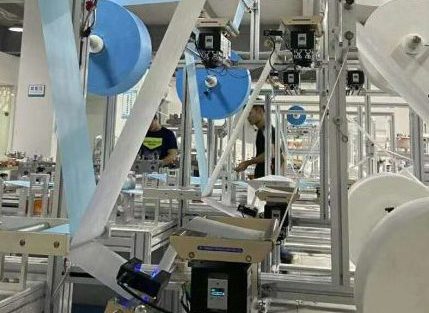
Traditional aircraft assembly relied heavily on skilled technicians spending thousands of hours drilling, riveting, and aligning parts. While craftsmanship remains vital, automation now handles repetitive tasks with superhuman consistency. For example, automated drilling systems can complete thousands of holes per day with tolerances under 0.01 inches, eliminating human error and reducing rework by up to 90%.
**Precision Engineering Meets Artificial Intelligence**
At the heart of this transformation lies the marriage of robotics and AI. Advanced systems now use machine learning to analyze vast datasets from previous assemblies, predicting potential bottlenecks or defects before they occur. Sensors embedded in tools and machinery collect real-time data on torque, pressure, and alignment, feeding it into centralized platforms for instant analysis.
Take the example of wing assembly—a process once requiring weeks of manual adjustments. Automated guided vehicles (AGVs) now transport wing sections to designated stations, where robotic arms equipped with laser-guided systems position components within 0.001 inches of perfection. AI algorithms cross-reference 3D models with sensor data to ensure every rivet and seam meets strict aerodynamic specifications.
**Collaborative Robotics: Humans and Machines as Partners**
Contrary to fears of machines replacing humans, automation is creating new opportunities for collaboration. Cobots (collaborative robots) work side-by-side with technicians, handling heavy lifting or hazardous tasks while humans focus on quality control and complex decision-making. For instance, a cobot might hold a 200-pound composite panel in place while a technician performs final inspections using AR-assisted visualization tools.
This synergy extends to training. Virtual reality (VR) simulations now prepare workers for real-world scenarios, from operating robotic systems to troubleshooting assembly line glitches. Trainees can practice installing landing gear or wiring systems in a risk-free digital environment, accelerating onboarding by 40% compared to traditional methods.
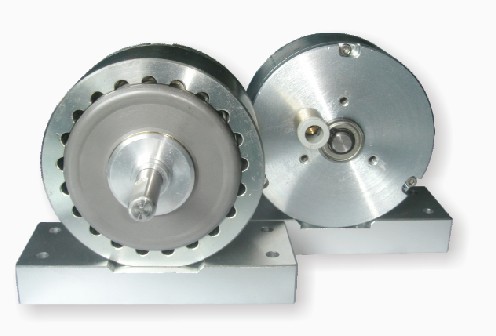
**Sustainability Takes Flight**
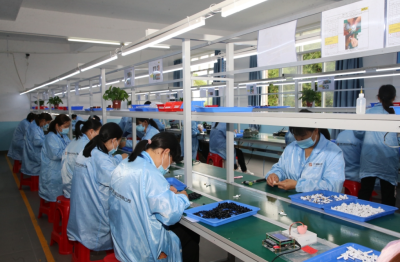
Aircraft automation isn’t just about speed and accuracy—it’s also a game-changer for sustainability. Automated systems minimize material waste by optimizing cutting patterns for composite materials, reducing scrap by up to 35%. Energy-efficient robotics consume less power than traditional machinery, while predictive maintenance algorithms extend equipment lifespans by identifying wear-and-tear before failures occur.
Moreover, lightweight automation tools enable the use of advanced materials like carbon-fiber-reinforced polymers. These innovations contribute to fuel-efficient aircraft designs, directly supporting the industry’s goal of achieving net-zero emissions by 2050.
** motor test : The Autonomous Assembly Line**
A leading aerospace manufacturer recently unveiled a fully autonomous fuselage assembly line. Here’s how it works:
1. AGVs deliver pre-fabricated sections to a climate-controlled clean room
2. Computer vision systems scan each component for micro-imperfections
3. Swarm robotics teams simultaneously work on different sections, coordinated by a central AI
4. Automated inspection drones perform 360-degree quality checks
5. Blockchain-based documentation tracks every step for regulatory compliance
This system reduced assembly time by 60% while achieving a 99.98% defect-free rate—a previously unimaginable feat in aerospace manufacturing.
**The Future: From Factories to Flying**
Emerging technologies promise even greater advancements:
- Quantum computing for ultra-complex aerodynamic simulations
- Self-healing smart materials that detect and repair micro-fractures
- 3D-printed engine components with lattice structures lighter than ever before
- Digital twin technology enabling real-time fleet performance monitoring
As drones and urban air mobility vehicles enter mainstream markets, automated assembly will become crucial for scaling production safely and efficiently.
**Conclusion: Engineering Tomorrow’s Skies Today**
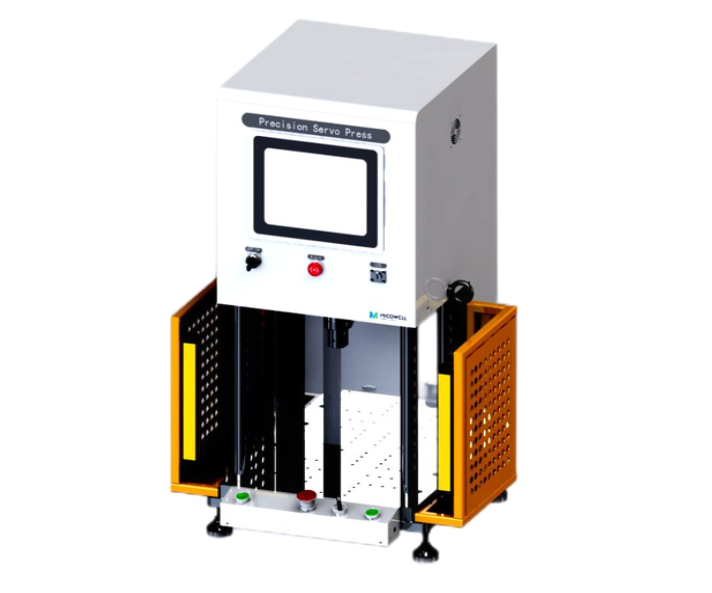
The quiet hum of robots working in harmony with human experts isn’t just noise—it’s the sound of progress. Aircraft assembly automation represents more than technical upgrades; it’s a fundamental reimagining of how we build the machines that connect our world. By embracing these technologies, the aerospace industry isn’t just crafting better planes—it’s paving the way for safer, cleaner, and more accessible air travel for generations to come.
The runway to the future is clear. With automation as our co-pilot, we’re not just building aircraft—we’re constructing bridges to a smarter, more efficient tomorrow. 🛫🔧🌐