In the fast-paced world of industrial innovation, precision and efficiency aren’t just goals—they’re necessities. Enter the **electric motor dynamometer**, a game-changing tool redefining how engineers and manufacturers test, optimize, and validate motor performance. Whether you’re developing cutting-edge EVs, industrial machinery, or renewable energy systems, this technology holds the key to unlocking unprecedented accuracy and reliability. Let’s dive into why dynamometers are the unsung heroes of modern engineering—and how they can transform your workflow.
~~~
WHY ELECTRIC MOTOR DYNAMOMETERS MATTER 🛠️
Imagine building a high-performance electric vehicle without knowing if its motor can handle real-world stress. Or designing a wind turbine without verifying its efficiency under variable loads. Scary, right? That’s where dynamometers come in. These systems simulate real operating conditions, measuring critical metrics like torque, speed, power output, and energy consumption.
Traditional testing methods often rely on approximations or fragmented data. A dynamometer, however, provides a controlled environment to:
- Validate design prototypes with **laboratory-grade precision**
- Identify inefficiencies before mass production
- Extend equipment lifespan by stress-testing components
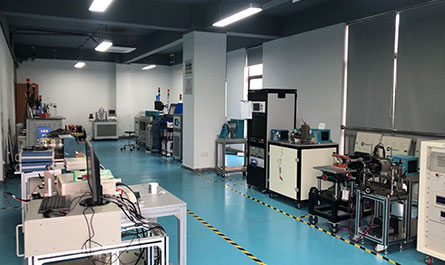
- Comply with international performance standards (ISO, SAE, etc.)
The result? Fewer costly recalls, faster time-to-market, and products that outperform competitors.
~~~
CHOOSING THE RIGHT DYNAMOMETER: A BUYER’S CHECKLIST 🔍
Not all dynamometers are created equal. Here’s what to consider when selecting a system tailored to your needs:
1. **APPLICATION-SPECIFIC DESIGN**
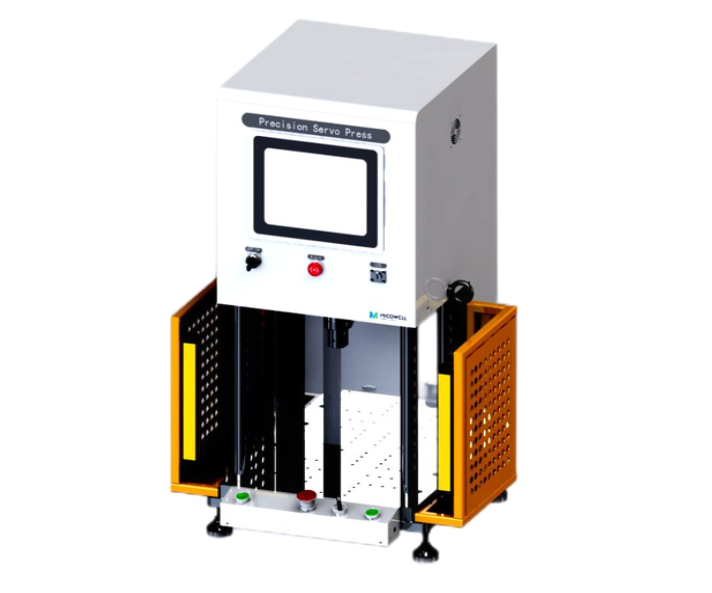
Are you testing small drones or massive marine engines? Dynamometers range from compact 5kW units for R\u0026D labs to multi-megawatt systems for heavy industries. Match the device’s capacity to your maximum torque and RPM requirements.
2. **DYNAMIC RESPONSE TIME**
High-speed applications (e.g., aerospace) demand ultra-responsive controls. Look for motor test with sub-millisecond feedback loops and adaptive algorithms that mimic sudden load changes.
3. **ENERGY RECOVERY FEATURES**
Modern regenerative dynamometers can recycle up to 90% of absorbed energy back into your facility’s grid—slashing testing costs and aligning with sustainability goals.
4. **SOFTWARE INTEGRATION**
Seamless compatibility with tools like MATLAB, LabVIEW, or Python APIs allows automated data logging, real-time analytics, and custom test sequences. Bonus points for cloud-based dashboards for remote monitoring!
5. **SCALABILITY**
Modular systems let you upgrade sensors or software without replacing the entire setup—a smart choice for growing enterprises.
~~~
BEYOND TESTING: UNEXPECTED USE CASES 🌐
While dynamometers shine in motor validation, their versatility extends further:
🧠 **AI TRAINING**
Machine learning models for predictive maintenance thrive on high-quality torque and vibration datasets—exactly what dynamometers provide.
🌱 **RENEWABLE ENERGY OPTIMIZATION**
Test wind turbine generators under simulated storm conditions or calibrate solar tracking systems for maximum efficiency.
🏎️ **RACING TECH INNOVATION**
Formula E teams use dynamometers to fine-tune regenerative braking systems, squeezing every joule of energy from lap simulations.
~~~
THE HUMAN SIDE OF TECHNOLOGY 🤝
Behind every dynamometer is a story of problem-solving. Take OceanTech Engineering, which reduced offshore pump failures by 68% after discovering harmonic vibrations during dynamometer tests. Or VoltBike, an e-mobility startup that cut development cycles by 40% using automated load cycling.
“We thought we’d hit a wall with our motor’s overheating issue,” says VoltBike’s lead engineer. “The dynamometer not only pinpointed the flaw in our cooling design but also helped us simulate fixes virtually. It was like having a crystal ball for engineering.”
~~~
FUTURE TRENDS: WHERE INNOVATION IS HEADED 🚀
1. **EDGE COMPUTING INTEGRATION**
Next-gen dynamometers will process data locally via onboard GPUs, enabling real-time AI diagnostics without latency.
2. **DIGITAL TWIN SYNCHRONIZATION**
Pair physical tests with virtual motor replicas to predict wear-and-tear patterns over decades of simulated use.
3. **AUTONOMOUS TESTING**
Imagine a dynamometer that self-adjusts parameters based on live data—no human intervention needed.
4. **HYPER-CUSTOMIZED SIMULATIONS**
Test motors in digitally recreated environments, from Arctic temperatures to Martian dust storms.
~~~
CONCLUSION: POWERING PROGRESS, ONE TEST AT A TIME 🔋
Electric motor dynamometers aren’t just tools—they’re partners in innovation. By bridging the gap between theoretical designs and real-world performance, they empower engineers to push boundaries while minimizing risks. As industries race toward electrification and automation, investing in robust testing infrastructure isn’t optional; it’s the bedrock of sustainable success.
Ready to elevate your testing capabilities? Explore our range of smart dynamometers today—and let’s engineer a future where every motor delivers on its promise. 🎯
~~~
[Discover how our ISO-certified dynamometer solutions can accelerate your projects. Schedule a demo or download our technical whitepaper now!]
~~~
Still have questions? Our team of application engineers is here to help—because even the most advanced technology works best when paired with human expertise. 💬
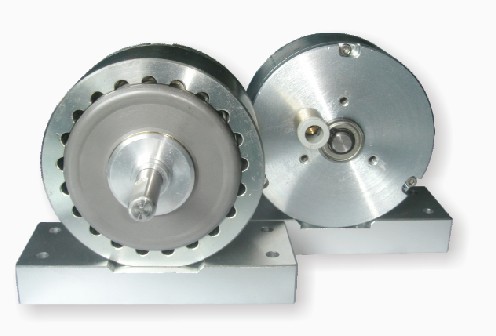